Automating end-of-line packing at Beans Coffee
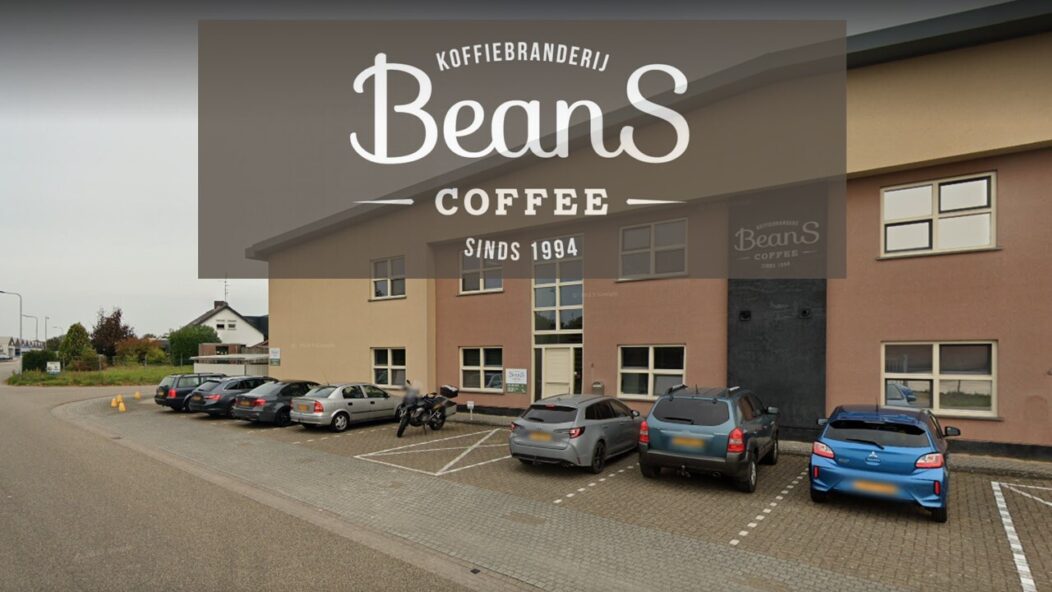
'Everyone wants to work at line one'
Article in VM - "Verpakkings Management"
By Harry van Deursen
Paul de Haan opened a coffee shop in Roermond in 1994. From a small coffee roaster, he grew to coffee roaster Beans Coffee in Ittervoort, which produces more than 10,000 kilos of coffee every day for the private label market. Last May, the company automated one of its four packaging lines with a CPS case packer. “An automation that leaves the operators wanting more.”
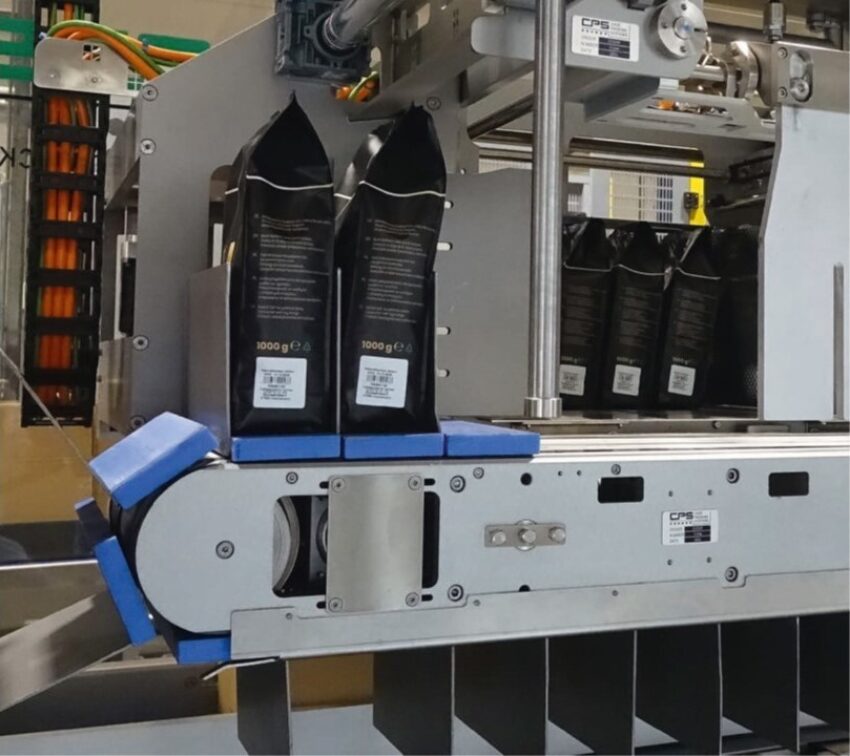
“The shopping street in Roermond was regularly blue with smoke from my coffee roaster,” says Paul de Haan, when he looks back on the origins of his company. 'The store was a great success, but the combination of a store and coffee roasting company in one was no longer sustainable due to environmental regulations. We moved to an industrial area and switched to a 25 kilo burner. That was also the starting signal for my private label coffee roasting company Beans Coffee. We grew fast and in 2004 we had to move to our current building, where we have one 50-kilo burner and three 120-kilo burners. Every year we supply 1.8 million kilos of coffee to specialty coffee shops, supermarkets and vending operators who install coffee machines at companies. The quality varies from competitively priced robusta coffee to exclusive South American arabica coffee, straight from the farmer.'
Four packaging lines
After the raw coffee beans have been slowly roasted in drums at about 210 degrees until roasted, golden brown and deliciously smelling coffee beans, they are sent to the packaging department. There they are packed in 250 grams, 500 grams or one kilo on one of the four packaging lines. Packaging
starts with the weighers above Goglio's vertical form, fill and seal machines that dump the beans into the forming tube after which they fall into the vertically shaped block bottom bags. After closing the bags, they go via a discharge conveyor to the packers who manually put the bags in boxes and close and palletize the box. The growing demand for coffee beans forced De Haan to make line one run faster. However, this ran into problems with the final packaging. 'The packaging machines produce 30-40 bags per minute. Two packers cannot handle that. Expand to three to five packers was not an option, so we chose to automate line one first with a CPS case packer.'
Choosing CPS
The choice for Case Packing Systems (CPS) from Stramproy was quickly made. The machine builder is a ten-minute drive around the corner and it just so happened that CPS had a case packer under construction for another coffee roaster in the Netherlands. “I was just driving back from that other coffee roaster when Paul called,” says RobertEvers, area sales manager at CPS. 'So he could immediately go this way for a touch and feel. Two days later the deal was completed and last April we installed the GCL case packer with a case erector and closer.”
Perfect match
“The GCL is the perfect match for vertical packaging of coffee bags,” says Evers. 'This case packer was actually developed for display boxes. The bags in the display boxes are packed upright, which is also a requirement in the coffee market. Many companies want the bags to be packed as tightly as possible in the box, but in the coffee market the bags must remain neat and can therefore not be packed too tightly in the box. In addition, the coffee beans must still be able to outgas in the bag and that works better standing up than lying down.' Furthermore, according to Evers, the GCL is characterized as a compact, user-friendly machine that is easily accessible for size changes and maintenance thanks to two large opening doors on the side. The machine can be adjusted quickly and easily, De Haan confirms. “Our operators converted the machine within a few minutes.” The capacity of the GCL is around 17 to 18 boxes per minute. Theoretically, the machine could process 140-160 bags per minute, but that depends on the machine in front of it. At Beans Coffee the speed is 20-25 bags per minute.'
Calm in the workplace
Just like coffee, automation 'makes you want more' and De Haan does not rule out expanding even more lines in the future. 'We started with line one, because that's where the largest orders go. Now you see that all colleagues in the packaging department want to work on line one," he says, laughing. 'And the person standing there often has a broad smile on their face, because the case packer takes away the physical labor. We have gone from two to one operator on that line. The machine is virtually trouble-free. All the operator has to do is check the bags that enter the line. It creates peace in the production hall. The next step we will take is to automate line two.'
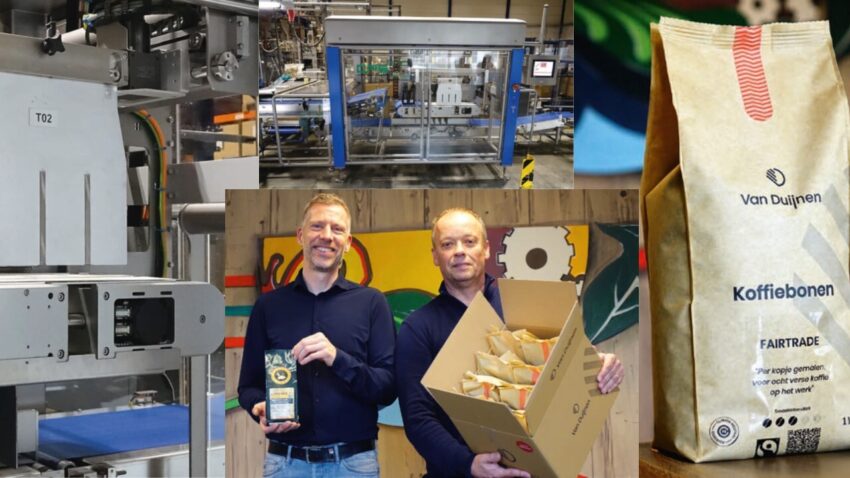