CP 201 casepacker in action for difficult frozen products
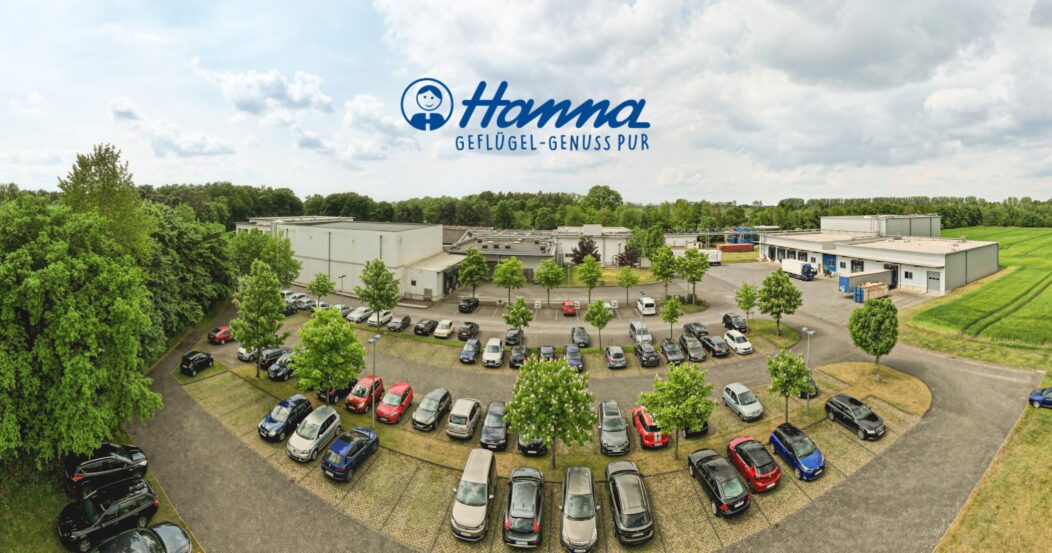
The chicken breast fillet in a crispy coating from Hanna is a crispy, tender treat for the palate. On the other hand, the automated packaging of the frozen poultry specialty with the rough and notchy breading is a tough one. The packaging specialists from CPS fought their way through and found a solution.
As a guest of the hotel, catering or community catering industry, almost everyone has eaten poultry products from Hanna-Feinkost AG from Delbrück. Over 100 different carefully refined poultry specialties delight the cooking professionals with a high degree of convenience and a reliable guarantee of success. Hanna obtains the fresh raw materials required for production mainly from the region. The poultry specialist seasons, marinates, fills, breads and partially cooks the meat products, which are deep-frozen after processing and then packaged. A specialty of Hanna is the chicken breast fillet in a crispy coating. The company produces the schnitzel with the crispy cornflakes breading in various weights from 100 g to 180 g. They are packed in a large tubular bag in cartons of 3 kg each. "These products are difficult to pack," says Bernhard Wissing, CEO of Hanna-Feinkost AG. “The flat shape makes it very bulky. The coarse-grained breading prevents them from slipping against each other and the schnitzel get caught. That's why we've always packed the product by hand in the past."
The employees used to place the 3 kg bags with 17 to 30 schnitzels, depending on the calibration, in the box. The manual shaking and distribution of the crispy specialty in the bag so that the carton could be closed was extremely stressful. "Our ladies from the packaging department were very adept at it," says Wissing. “But in the long run they had an unreasonable physical strain that was too much. It couldn't go on like this.”
The first tests at Case Packing Systems (CPS) in Stramproy/Netherlands showed how well the women mastered their work. Henri Veltmans, Sales director at the company, explains: “To understand the process, we first tried to understand how manual packing works. None of us managed to distribute the schnitzels in the bag in such a way that the box could be sealed.”
The automation didn't work right away either. Only when a cardboard box was used that was a little longer and a few millimeters higher did the packaging specialists succeed. "Usually we can pack more kilograms per cubic meter with our systems than is possible by hand and also than our competitors can,” says Veltmans. "Hanna's crispy schnitzel is the only case in which we had to increase the carton volume a little." For other small-piece products, such as Hanna's chicken crossies, which also run on the system, the carton volume could be reduced.
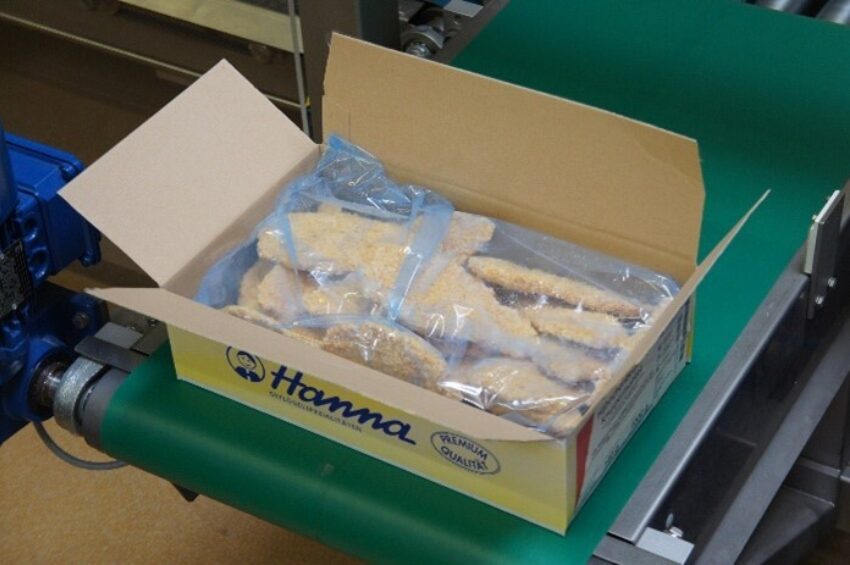
Special carton size
The special carton size doesn't make packing the schnitzel any easier either. In the deep-freeze industry, CPS mostly works with larger units. "We usually deal with 10 kg boxes," says Jochen Schöbel, the company's Area Sales Manager Germany. "It's rarely 5 kg, but there are also 15 kg cartons. The 3 kg boxes for bulk consumers, which Hanna mainly uses, simply don't offer enough leeway. If the crispy schnitzel were packed in 10 kg boxes, that would not be a problem. Here the carton would have the same format as in the case of final packaging by hand.
After a few attempts, a cardboard solution was found that was satisfactory for everyone involved. The packing process now runs smoothly. The products come from VFFS machine to the casepacker on a conveyor belt. As the first station, the bags go through a metal detection. Then they are equalized so that the contents are evenly distributed and the bag is vented. Next, a checkweigher with a reject checks the weight. From here the bags are fed to the casepacker, which is equipped with automatically operated discharge flaps and a patented bag feed. The bag infeed system consists of two vertical belts that are adjustable in width and thus reduce the bag volume as the bag passes through to the case packer. The bag enters the carton below through bombdoors. Now it is weighed again and incorrectly filled boxes are rejected. "Because we first weigh the bags and then the entire case, there is no possibility of incorrect fillings being delivered," says Veltmans. The content of the box are further compacted at an additional vibrating station. Finally, the box is closed by tape and the labels are applied.
In the case of format changes for other products, the machine operator only needs to select the desired program in the control menu and manually switch over two levers on the carton erector and the packing process continues. Wissing says: "We can now pack about 80 of our 100 product variants with the case packer."