Adapting to the demands of the fresh frozen product industry. (Frost Service Venlo, AGF Primeur)
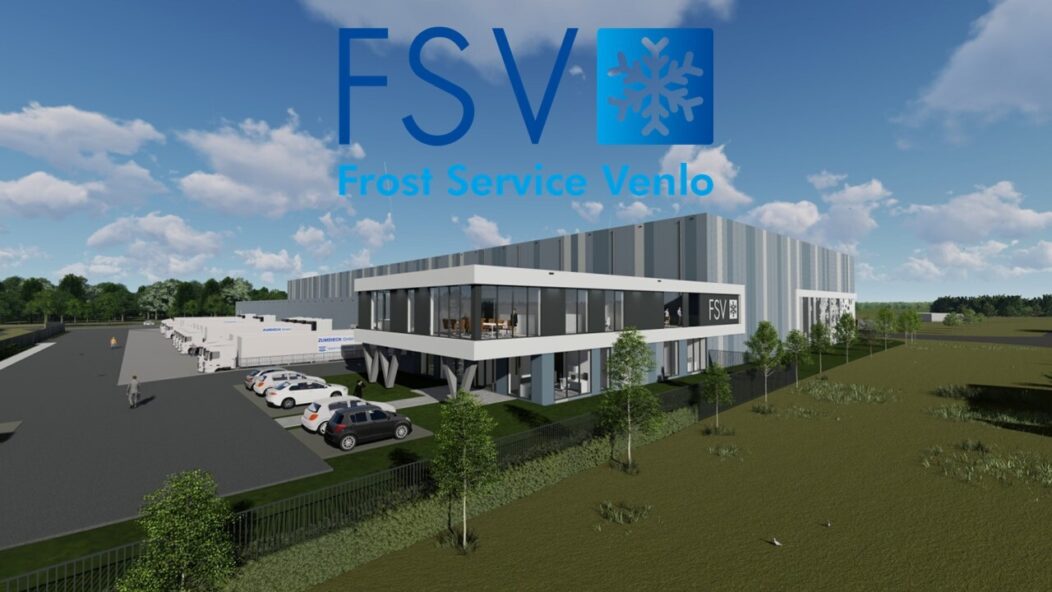
“We had outgrown our jacket,” says Ron Steinhage, site manager from Frost Service Venlo – that produces deep-frozen products by order processed, packaged and stored – about the new building at Green Port Venlo. Although the availability of materials and people due to the outbreak of the conflict in Ukraine – Russia came under pressure, the building is now since this year January in operation.
The new building offers space for the growth that Ron also expects for the frozen food category in the future. “The constant demand for fresh frozen products remains. Since I started in the frozen food world in 1990, I have not experienced a single year where there was less turnover or tonnage in frozen fruit and vegetables than the year before. And in 2023, the category is still growing.”
Industry 4.0
In the context of Industry 4.0 – the emergence of digital industrial technology – CPS and FSV are joining forces to raise the service level of the packaging lines. As an example, Henri mentions a motor that automatically reports this if it starts to use more power. He sees that many companies have scaled down their technical services, which means there is a need for more service. “That is why we want to offer services that go that little bit further. Now we often only get a call when something is broken. You can also prevent this with a system that, for example, keeps track of how often a cylinder moves. If it can move an average of a million, we can now issue a warning when its lifespan has expired. That is the next service, that we can identify and adjust such matters.”
WAREHOUSES ARE FULL
He does see changes in the market as a result of the corona crisis and the conflict in Ukraine. “It is a very crazy purchasing market. We've seen strange scenes early in the war, with prices going up like crazy. Now you see that many warehouses are full and many parties are reluctant causing prices to plummet. As a result, the market is hesitant and little is bought in due to falling prices.”
The products that Frost Service Venlo packs mainly find their way to retail, with about 70 percent finding its destination across the German border. In addition, Ron sees that where previously supermarkets mainly purchased products per box, there is now a great demand for assortment boxes with instead of, for example, only bags of strawberries also bags of cherries and raspberries. “A mix box is chosen, which is easier in terms of order unit and ensures that there is not a lot of volume for one product.” And Ron notes that the limited availability of labor also plays a role in retail. “It has to be ready-made. There is a demand for boxes that can be easily shaken empty in the freezer, so that the staff in the store - which is of course also scarce there - have much less work and can do much more per hour. to fill."
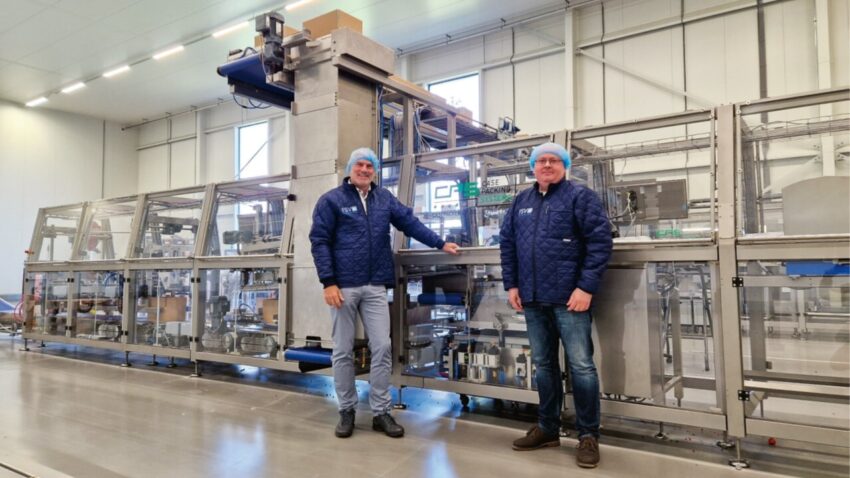
HIGH LEVEL OF AUTOMATION
“Filling an assortment box, for example, places demands on the packaging machines,” says Henri Veltmans, Sales Director of Case Packing Systems (CPS) – which focuses on packaging lines, for individual frozen products – which was involved in the development of the packaging lines for the new building. “We were able to automate the mix packaging; where there are two assortments end up in one box. So now the installation offers the possibility to pack mix packs as well as mono packs and loose product. In addition, the installation is able to fill octobins automatically. The degree of automation is therefore very high.” Something that FSV is happy with, because efficiency is been one of the central themes in the development of the new factory, says Ron. This also applies to the packaging process. While fresh products are much more fragile and need to be protected in trays, efficiency and avoiding air packing are important for frozen products, Henri explains. “You want to pack as many kilos per cubic meter of packaging as possible to increase the efficiency of the packaging process.” He indicates that this offers opportunities to save on cardboard and logistics. “The entire logistics chain runs at -22˚C. Not only production, but also storage and transport cost a lot of money. If you can do that a few percent better, then you are very sustainable busy because you save in the chain.”
BIG SAVINGS
“The savings can be substantial,” Henri notes. "In addition to the savings on labour, you save - and that can amount to 25,000 euros per line - costs in the chain through more favorable storage and transport through lower boxes." Ron also mentions the savings on labor and lower cartons as an important aspect. "The availability of labor is a drama, so if you can do something about it in the chain, that is very good. With the new packaging line we save two staff members and the packaging quality is better than manual packaging. No one can compete with the continuity of a machine.”
Anniversaries
Both FSV and CPS have a party to celebrate this year. FSV has existed for 20 years and CPS is ticking 35 years. To mark this anniversary, CPS is organizing open days from 22 to 24 June. In June, FSV will reflect on this milestone in its own circle and with the German head office. In addition, it has an open day for relations in the planning.
Ron also sees that sustainability is an important aspect for retail, which has also been implemented as much as possible in the new building. “We get questions about this every day. With the new building we can demonstrably say that we use less material and have a faster passage of products. In addition, we no longer package air, which means that we can use smaller boxes and put higher volumes on a pallet. Efficiency goes up and costs go down. That's the only way to keep your head above water at the moment and you actually try to take that with you across the board.” Ron sees that many of these small interventions together can yield serious savings. “In cubic meters, the new building is three times the size of the previous building, while we don't even have twice the power load.” (MW)