CP 201 Gravity Case Packer
The CP 201 gravity case packer is specifically designed for packing bags into cases horizontally, with maximum speed and efficiency. This machine is widely used for products such as frozen fries, vegetables, meat, and fish. With the CP 201 case packer, significantly more kilograms per cubic meter can be packed compared to manual processing. This leads to higher productivity and optimal use of available packaging space.
Request for quoteFunctional description
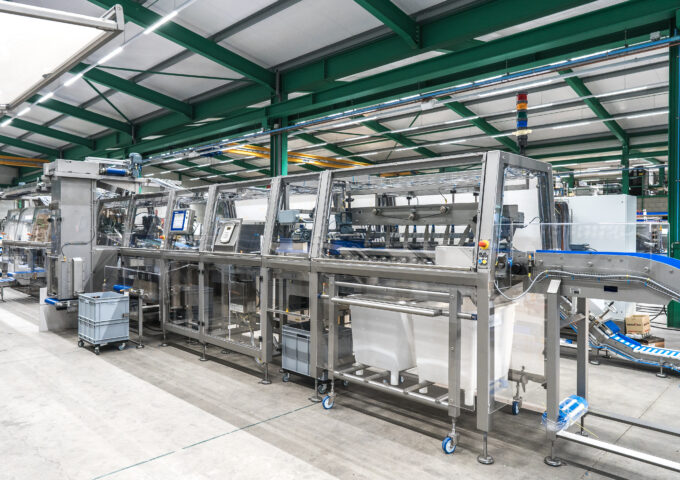
Packing bags horizontally in cases or crates
The CP 201 gravity casepacker packs flexible bags horizontally in cases/crates, according pre-programmed packing patterns. The bags are centered at the infeed and can be turned for creating the correct packing pattern. The bags can partially overlap. A row of bags is guided into the case by bomb doors. Before the bags being packed compacting will take place. The CP 201 casepacker can be combined with many options to make a customer required packingline.
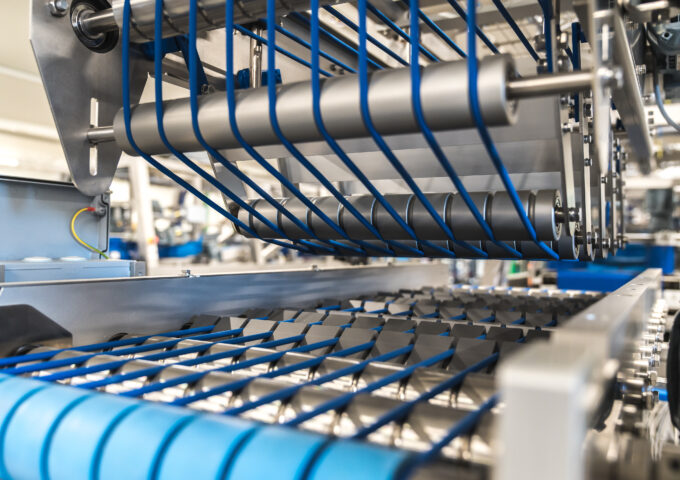
Rumbling station
After the bags are being taken over the bags are flattened at the rumbling station. Loose product detection will take place at the same time. Open bags will be rejected by our retract belt. Optional the air deflation unit can be added to this station.
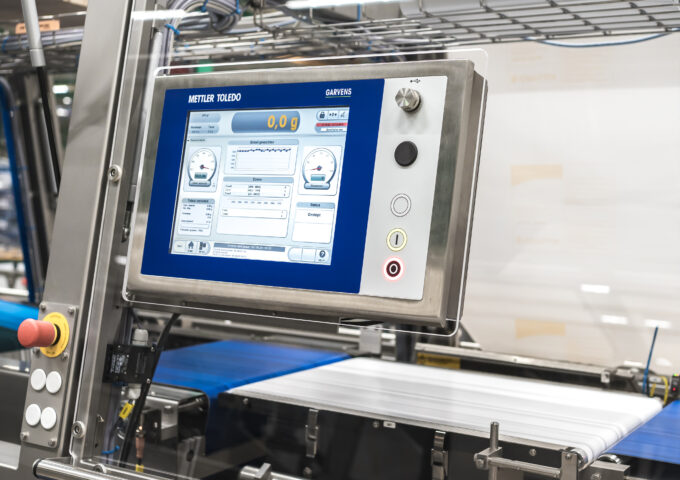
Easy integration of non CPS components
Our CP 201 can be easily equipped with a bag control weigher, metal detector and or X-ray detector.
Some of these components can even be integrated into our own menu. Which means, a product change is controlled via our HMI. The reject of wrong weights and or detected bags happens over our CPS retract belt.
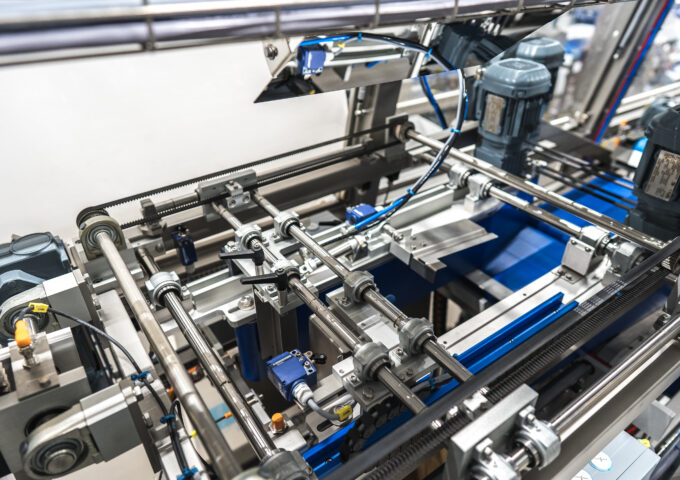
Compacting group
The vertical belts of the compact group above the bomb doors can move independently of each other and, moreover, move towards each other or from left to right, bringing the rows of bags into any desired position above the bomb doors.
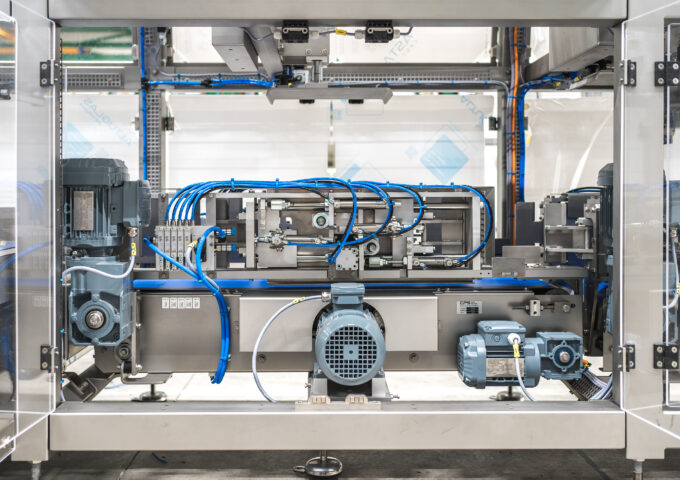
4 side compacting
With the 4-dimensional compacting group, the case is locked on 4 sides and pressed from above while vibrated. Vibration frequency and duration is menu controlled. The top plate is laser-controlled in height and measures the height of the product in the case. If the product is too high in the case, it will be removed out from the line at the case weigher.
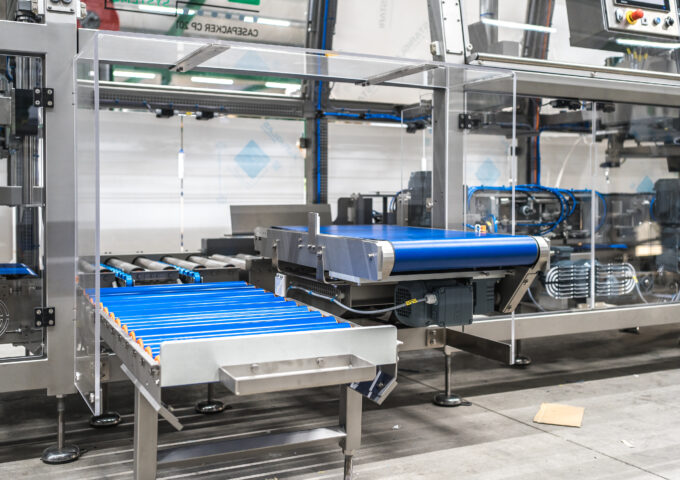
Case checkweigher
After the case has been filled and compacted, it is transported to the case weighing station where static weighing takes place. Wrong weights cases are automatically removed from the line and rejected on the roller conveyor. Due to the case re- infeed belt (optional), the cases can be automatically brought back into the line after manual correction.
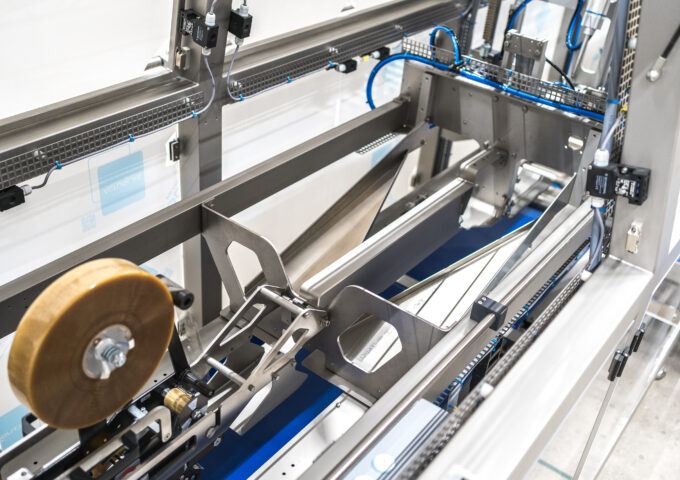
Case closer
The CPS case closer has been specially developed for closing American style cases either with tape or hot melt. During closing the case is vibrated and pressed to get a perfectly closed case to guarantee problem-free palletising. This closer can handle fefco 201 (tape/hotmelt) and 209 (hotmelt) cases. It's completely menu controlled and the changeover between tape and hotmelt can be done toolless in just a few minutes..
Features
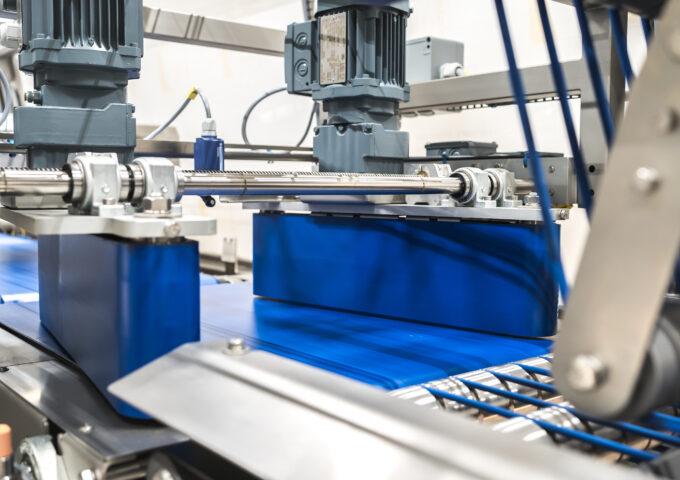
CP 201 packing more product per m³!
- Proven technology.
- We pack more product/m³!
- tot 160 producten per minute.
- Flexible in packing patterns.
- Easy to operate. Wizard for programming and menu controlled.
- Maintenance friendly, easy accessibility.
- Standard remote access.
- Build out of stainless steel and aluminium components.
- Reduction of downtime. Menu controlled.
- Easy integration / combination of third party equipment.
Technical properties
Product data CP 201 Gravity Case Packer
Dimensions | Length: 3800mm; Width: 1200mm; Height: 2000mm |
Product infeed height | 1200mm |
Case in- and outfeed height | 450mm |
Electrical supply | 3Phase 400V + N + PE 50Hz 3,1kW 16A |
Compressed air supply | 350 Nl/min, 6bar |
Shipping weight | 1500kg |
Case dimensions | Length: 150 - 600mm; Width: 150 - 400mm; Height 100 - 540mm |
Capacity | 160 products/min; 20 cases/min |